News
Short Path Fractional Distillation
Short path fractional distillation is a special liquid-liquid separation technology. It is different from traditional distillation which relies on the separation principle of boiling point difference, but relies on the difference in the mean free path of molecular motion of different substances to achieve separation. When the liquid mixture flows along the heating plate and is heated, the light and heavy molecules will escape from the liquid surface and enter the gas phase. Since the free paths of the light and heavy molecules are different, the molecules of different substances move different distances after escaping from the liquid surface. If a condensing plate can be installed properly, light molecules can reach the condensing plate and be condensed and discharged, while heavy molecules can’t reach the condensing plate and be discharged along the mixed liquid, thus achieving the purpose of material separation.
Short path fractional distillation is a thermal separation process that works at an absolute pressure of 0.001~1mbar (0.1~100Pa). Its lower boiling temperature is very suitable for heat-sensitive and high-boiling substances.
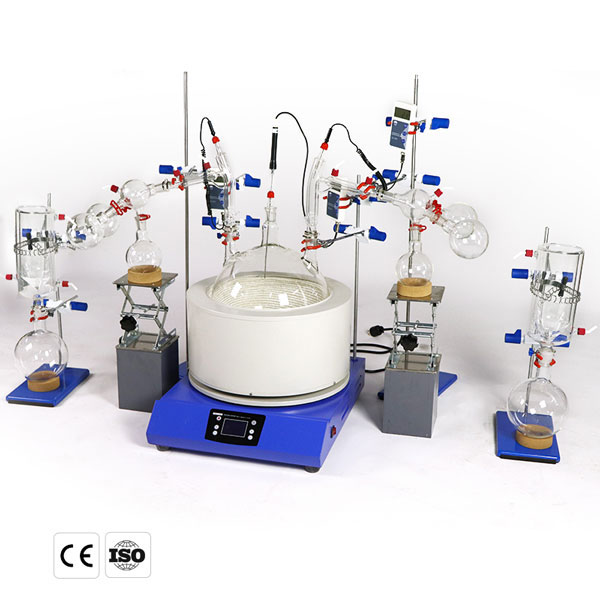
The principle of short path fractional distillation
From a microscopic point of view,
Our gas-liquid interface is not calm. Molecules in the liquid will jump out of the interface for a short time. A small part of the molecules that jump out of the interface have high kinetic energy and can diffuse into the gas phase. Most of them are due to the interaction with other molecules during the diffusion process. After the impact loses energy, it returns to the liquid phase. In this way, a diffusion layer will be formed near the gas-liquid interface, and the molecular density of this layer is between the gas phase and the liquid phase. The thickness of the diffusion layer is related to the degree of vacuum and temperature. If the degree of vacuum continues to increase, the frequency of molecules being hit will become lower and lower, so that the thickness of the diffusion layer will continue to increase, and the proportion of diffusion into the gas phase will also increase greatly. . If the liquidus temperature is high, the molecular energy is high, and the thickness of the diffusion layer is also increased. Finally, at the boiling point, all the liquid molecules on the gas-liquid interface have the ability to diffuse into the gas phase, and at this time it can be considered that the thickness of the diffusion layer can reach the entire gas phase.
From the above process, it can be seen that whether it is vacuum distillation or atmospheric distillation, it is a balanced process, and the distillation process must be completed at the boiling point corresponding to the pressure. If there is a method that can separate the liquid when it reaches below the boiling temperature, then the temperature of the whole separation process can be further reduced, which is the meaning of short path fractional distillation. The specific implementation method is divided into two steps. The first step is to increase the vacuum, so that the thickness of the diffusion layer will increase. In the second step we put a cooling plate in the diffusion layer very close to the liquid surface. The role of this cooling plate is to allow a part of the kinetic energy to enter the diffusion layer, but the molecules that have no ability to diffuse into the gas phase cool down when they hit the plate. It is not necessary for these molecules to reach the boiling point to undergo the distillation process.
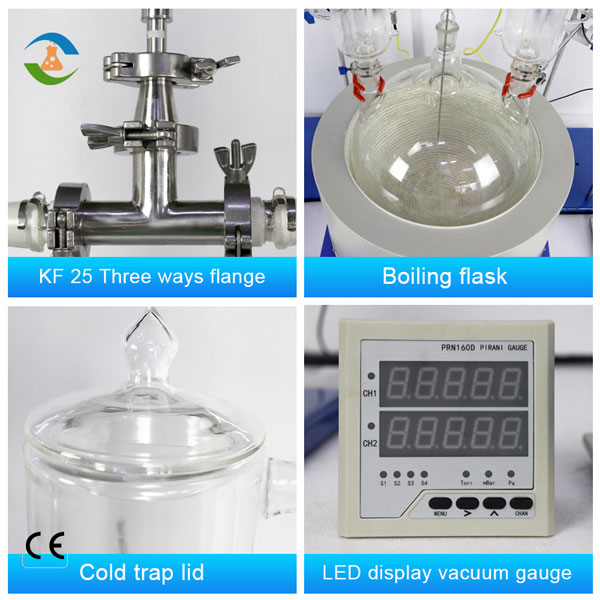
From a mechanical point of view,
The current molecular distillation machine generally adopts the scraper type, and the overall structure is roughly two concentric cylinders, the outer cylinder passes through the heating medium, and the inner cylinder passes through the cooling medium. The fluid flows down from the outer cylinder and is drawn into a liquid film by the scraper. Under the action of vacuum, the liquid in the liquid film moves to the gas phase, and is cooled down after contacting the cold inner cylinder to complete the separation process.
Advantages of FBL short path fractional distillation:
(1) High-speed electric needle valve is used instead of gas mass flowmeter
The high-speed electric needle valve used is a purely mechanical needle valve driven by a high-speed stepping motor. While greatly reducing the hysteresis error, it also shortens the overall response time to 800 microseconds. Quick and precise adjustment. The drive control only needs to use an analog voltage of 0-10V, and the overall structure is simple and reliable. Electric needle valves of various specifications have different gas flow adjustment capabilities, which can meet the vacuum control of distillers with different volumes. At the same time, FFKM perfluoroether rubber seals can be used to improve corrosion resistance.
(2) Use film capacitance gauge instead of Pirani resistance gauge and thermocouple gauge
The measurement accuracy of the film capacitance gauge used is much higher than that of Pirani resistance gauge and thermocouple gauge, and its accuracy can reach ±0.25% under any vacuum degree. Then for the vacuum measurement range of 0.001~1mbar (0.1~100Pa) in the short path distiller, you can directly choose a 1Torr film capacitance gauge to meet the full range of vacuum measurement. If you want to ensure the measurement accuracy in the range of 0.1~1Pa , You can also add a 0.1Torr film capacitance gauge. In this way, accurate measurement within the full vacuum range can be covered by two film capacitance gauges with different ranges.
(3) Use super-precision vacuum controller instead of ordinary precision PID controller
Using ultra-high precision PID vacuum controller. This ultra-high-precision PID vacuum controller has 24-bit AD and 16-bit DA, and uses double-precision floating-point calculations to achieve a minimum output percentage of 0.01%. This is an industrial PID controller with the highest technical indicators at home and abroad.
Using this vacuum controller can give full play to the precision advantages of the electric needle valve actuator and the thin-film capacitance gauge vacuum sensor, and this series of controllers has different models of single-channel and double-channel. The single-channel controller is a programmable PID controller, and its outstanding feature is that it can automatically switch between dual vacuum gauges with different ranges to realize full-range automatic control. The dual-channel controller is a fixed-point controller, and the two channels can independently control the vacuum degree and temperature.
Send Us Message
Your message was sent successfully.
Sorry!Something Went Wrong.