News
Short Path Distillation Unit
Short path distillation unit introduction
Before using the short path distillation unit, you must master its working rules and precautions in advance to avoid losses caused by misoperation during use. The following is a brief introduction to the short path distillation unit package.
A short path distillation unit is a distillation process in equipment operating under high vacuum. Short-range molecular stills are divided into three types according to the type of film scraper: rolling film type, sliding film type, and hinge film type. The appropriate film scraper is selected according to the viscosity and processing performance of the material.
The short path distillation unit is equipped with a laboratory water circulation pump and a vacuum pressure system of a short path distillation unit.
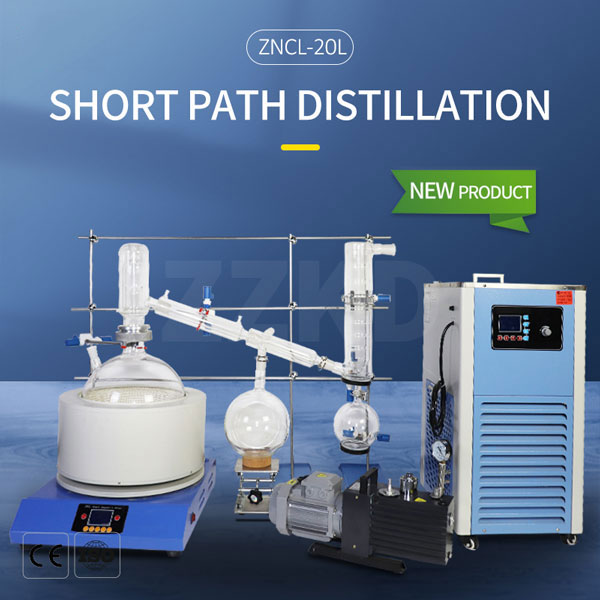
How short path distillation works:
The driving pressure for steam flow is the pressure difference between the boiling film and the condensing surface, and a small strain drop triggers the steam flow. Operation at 1 mbar and the need for a short distance between the boiling floor and the condensing surface nonetheless make stills made according to this principle known as short path. The short path still (molecular distillation) has a built-in condenser opposite the heated floor and delivers the working pressure up to 0.001 mbar.
Short path distillation is a thermal separation technique that works at pressures from 1 to 0.001mbar. Lower boiling point, suitable for heat sensitive, high boiling point materials. Its basic composition: a cylindrical cylinder with a heating jacket, a rotor and a built-in condenser; the wiper and the splash guard are precisely installed on the mounting body of the rotor. The built-in condenser is located in the center of the evaporator, and the rotor rotates between the cylindrical shell and the condenser.
The short path distillation unit consists of the outermost heated vertical cylinder, which houses a central condenser, and a wiper that rotates between the still and condenser.
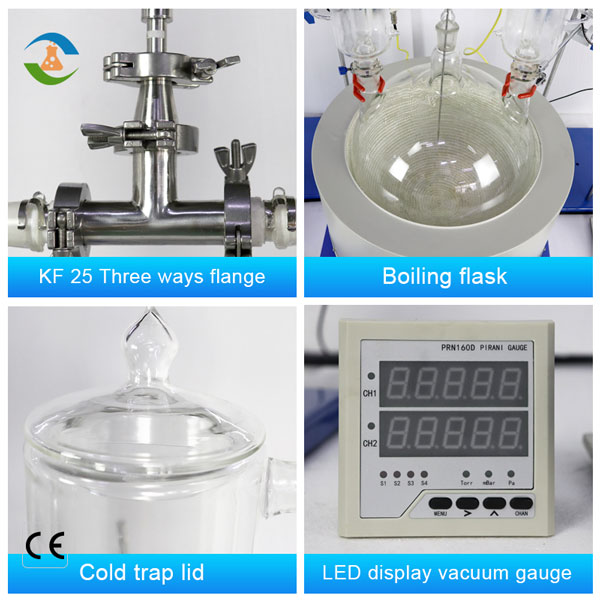
The distillation process is:
The material is fed from the top of the evaporator, and is continuously and evenly distributed on the heated floor by the material-liquid distributor on the rotor, and then the film scraper scrapes the fabric liquid into a slender, turbulent liquid film, which is pushed and eaten in a spiral shape. During this process, the light molecules escaping from the bottom plate of the heating surface condense into a liquid on the built-in condenser through a short distance with almost no collision, flow down the condenser tube, and pass through the evaporator on the back. The discharge pipe discharges; the residual liquid, i.e. heavy molecules, is collected in a circular channel below the heating zone and flows out through the discharge pipe on the facet. Short path stills are also better suited for molecular distillation. The molecules circulate from the heated floor to the condenser surface.
The short path distillation process can be divided into the following four steps:
1. Molecules diffuse from the mostly liquid part to the evaporated layer:
Usually, the diffusion price of the liquid part is the most important issue controlling the rate of molecular distillation, the thickness of the liquid layer must be reduced, because as much as possible is achieved and the flow of the liquid layer should be enhanced.
2. Molecules evaporate freely on the surface of the liquid layer:
Evaporation increases with increasing temperature, but separation problems sometimes decrease with increasing temperature. Therefore, a more economical and cheap distillation temperature should be selected under the premise of ensuring the thermal stability of the processed material.
3. Molecules fly from the evaporation layer to the condensation surface:
During the flight from the evaporating layer to the condensing layer, vapor molecules may collide with each other or with air molecules remaining between the two surfaces. Since evaporated molecules are much heavier than air molecules and most have the same path of motion, their collisions have little effect on the direction of flight and the speed of evaporation. Residual gas molecules are in a state of disordered thermal motion between the two sides, so the change of residual fuel molecules is the main problem affecting the flight process and evaporation rate.
4. Molecules condense on the condensation surface:
As long as there is a sufficient temperature difference between the cold and warm sides (generally 70~100°C), the type of condensation surface is cheap and easy to implement. Considering that the condensation step can be completed immediately, it is very important to choose an inexpensive type of condenser.
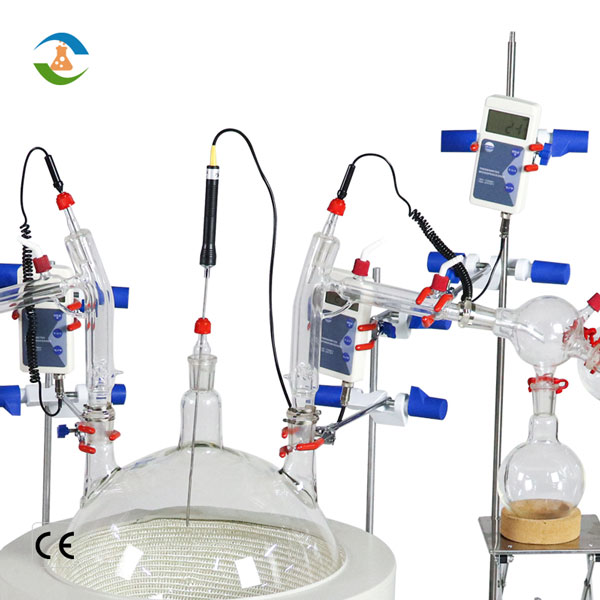
Craft Challenge:
Short path distillation uses vacuum to separate liquid mixtures. This is achieved by partial gasification of the components and separate recovery of the gas and distillation residue. In theory, with vacuum equipped, only non-condensable gases need to be removed from the system.
Process challenges stem from improper operation of the primary/secondary condenser, temperature instability, and excessive fouling of condensing surfaces. This will cause stripping or reactive gases to enter the vacuum pump, causing contamination problems, corrosion of the pump body, and eventually vacuum pump failure. In addition, since the pumped gas will pass through the pump, corresponding tail gas treatment equipment (such as tail gas condenser) should be equipped for collection to protect the environment.
Solution:
FBL has sufficient application knowledge, rich industry experience, advanced modeling technology, and professional design know-how. Using these advantages, FBL optimizes each customized vacuum system to achieve the best performance of the vacuum pump within the feasible range from the three aspects of reliability, economy and environmental protection.
In order to minimize the failure of the pump, a low-temperature interstage condenser, such as a liquid nitrogen cold trap, can be used to effectively protect the backing pump. For some small plants, effectively protecting the backing pump means avoiding serious contamination problems. Additionally, these traps can be used to collect valuable by-products such as fragrances.
And once the upstream protection mechanism of the pump fails, the FBL vacuum pump will not be affected by dirt, because its excellent liquid/solid handling capacity is more than enough to pump extremely polluting and corrosive gases. Therefore, the FBL vacuum pump can guarantee the longest normal production time and the least maintenance cost.
FBL vacuum solutions have been widely used in short-path distillation, a mild separation process, to deodorize, decolorize, and purify those expensive but heat-sensitive and easily oxidized products.
How to buy short path distillation unit?
Purchasing the most cost-effective short path distillation unit, an ideal short path distillation package solution is necessary, which will save pointless business expenses and time. FBL has highly specialized professionals who are always ready to help you with all your prepared short path distillation kit related questions. We sincerely look forward to your visit.
Send Us Message
Your message was sent successfully.
Sorry!Something Went Wrong.